Pelletron79 pelletron.htm is a leading provider of pneumatic conveying systems and components for the plastics industry. Pelletronsearch?q=pelletron introduces and displays new DeDusters and the pellcon3® conveying process at the NPE 2015 show in Orlando, Florida.
Pellcon3® – the new gentle conveying process
Visit our booth and see the new pelcon3® in operation. The pressure conveying process is designed for large conveying capacities, specifically for Compounders and Plastics Manufacturers, consisting of the three components STRANDPHASE®, Pellbow® and DeDuster®. Gentle conveying, low attrition and clean material are the main features besides the economical investment costs.
Pellcon3® sketch
The pellcon3 process consists of three major conveying components, STRANDPHASE® conveying, the special pipe bend Pellbow® and the DeDuster®. The system is in operation at the show.
STRANDPHASE® conveying
Working principle of the new, patented RC-series DeDuster®
Pellbow® working principle
This new process was developed for the plastics manufacturing and compounding industry. Selecting a pneumatic conveying system is important for economic and reliable operation of any plastics manufacturer or compounder. Poorly designed systems lead to plant-wide inefficiencies and high maintenance costs. When designing pneumatic conveying systems, many design parameters must be considered. The length of the system, numbers of elbows and varying material properties all have a significant influence on the determination and sizing of a pneumatic conveying system.
Cost savings with pellcon3®
Existing dense phase and dilute phase systems may be upgraded to incorporate pellcon3® technology. Upgrading an existing system to pellcon3® provides a quick return of investment. Besides the savings of 20% to 30% compared to dense phase conveying at new plant installations, pellcon3® provides lower operation costs and better product quality, which results in higher resin market prices.
Developed for injection molders – the new lightweight DeDuster®
Removing dust and streamers prevents the creation of black or weak spots in finished products and results in reduced scrap rates, higher quality parts and improved profit.
C-20 DeDuster® installed on Injection Molding Machine
The design:
The C-20 DeDuster® weighs 20lbs (9kg) and requires only 9.5in (240mm) for installation between the hopper loader and inlet hopper of an injection molding machine. It features stainless steel construction, 110 or 220V operation and only consumes 2-3CFM (3.4-5m3/h) compressed air at 20-30psi (1.5-2bar) pressure. The C-20 DeDuster® is designed for a nominal product flow rate of 50lbs/h (~20kg/h) at 30lbs/ft3 (560kg/m) bulk density. Flow rates up to 70lbs/h (30kg/h) are possible for products with higher bulk densities.
How it works:
The design of the C-20 builds upon the features of the proven mini-DeDuster® Series. The product inlet has an integrated agitator to reduce “bridging” and the Venturi design maximizes dust removal performance and minimizes carryover of good product into the dust collector. It operates with compressed air supplied directly from the plant air supply instead of from a separate fan.
Inside the unit, the compressed air is split into two air streams for optimal removal of dust and streamers, and an ionizer is used to release the electrostatic bond between the pellets and the dust. The cleaning air blows the removed fines and streamers into two mini-cyclones, which separate them from the air. The separated contaminants are collected in a clear dust collection box and the cleaned air is filtered and released to the atmosphere. For creation of a negative pressure in the entire device, outside air is pulled in through a filter-protected opening.
New DeDuster design for high capacity loading of up to 150t/h
XP-series DeDuster® with automated inlet device
Visit our booth and see the XP-360 DeDuster® with the new automated inlet device in operation.
Pelletron DeDuster XP360
Saving costs and simplifying the operation was the inspiration for this new development (patent pending). This DeDuster® feature was designed for cleaning large capacities of plastics pellets in Plastics Producer plants from 40,000 lbs/h (18 t/h) to 330,000 lbs/h (150 t/h) at bagging, truck and railcar loading. The new device eliminates the use of expensive and heavy rotary valves that are normally used for feeding product into the DeDuster®. The automated inlet deflectors move to adjust the product flow to the desired flow rate, evenly distribute product over the wash decks of the DeDuster® and can shut down the product flow completely. Rugged pneumatic actuators with integrated positioners move the inlet deflectors to any position based on a control signal from the plant DCS.
Pelletron at the NPE 2015 – Booth W3383
Pelletron at the NPE 2015
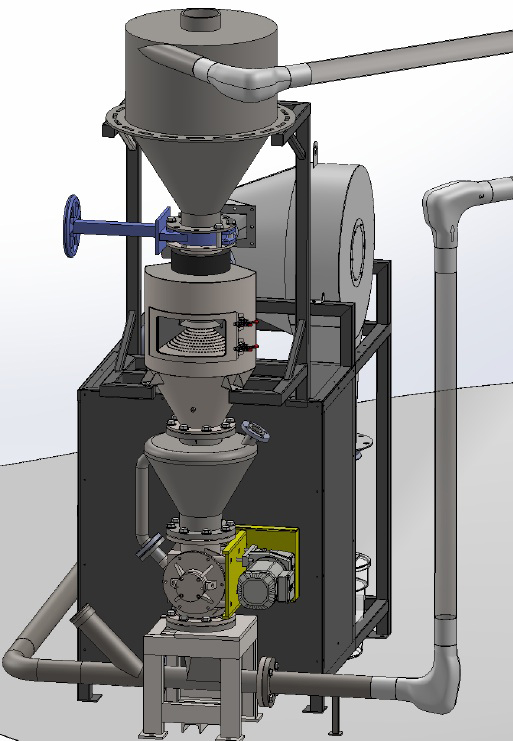

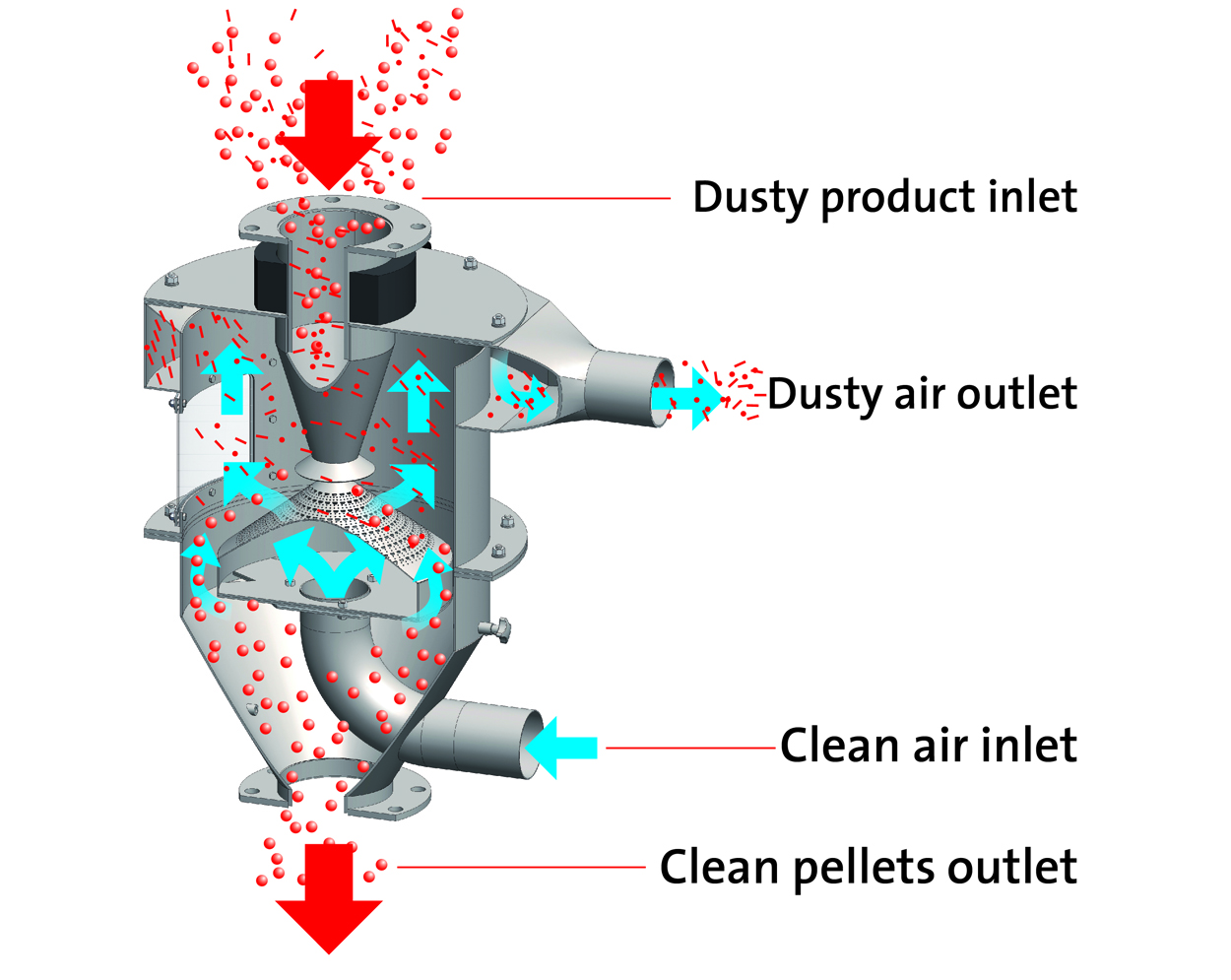
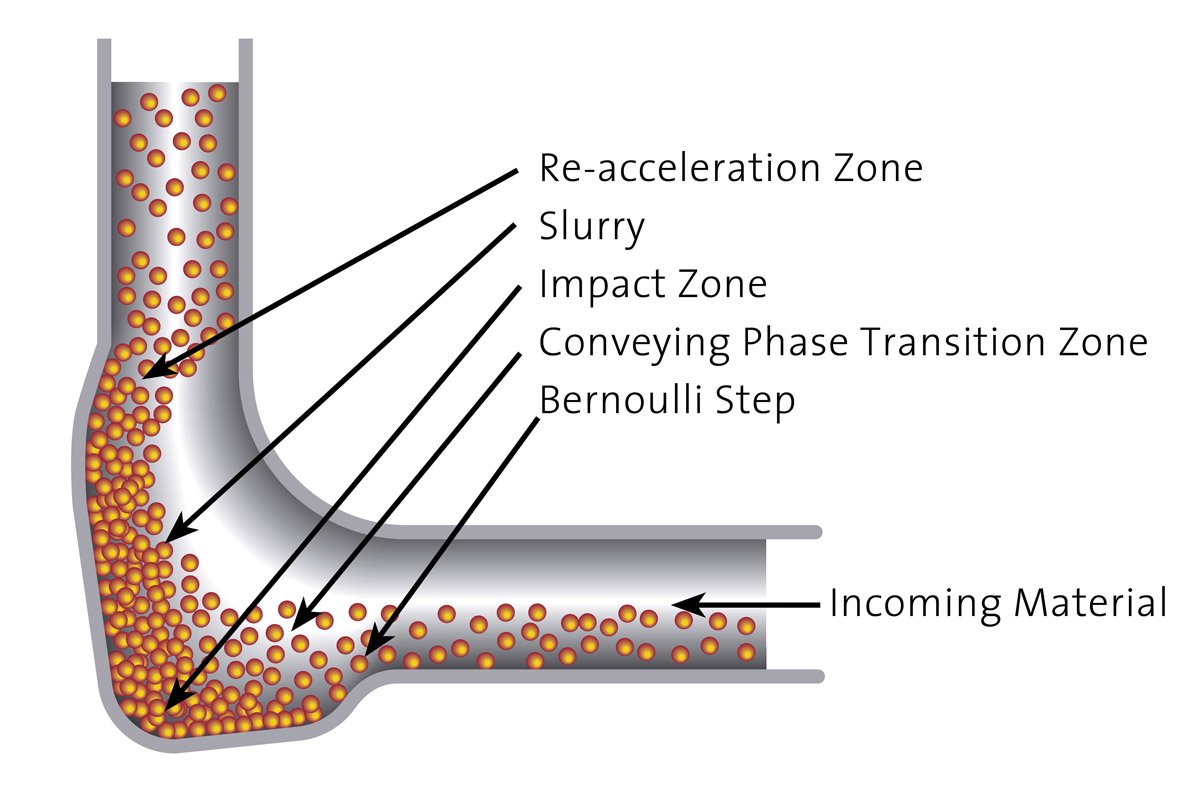
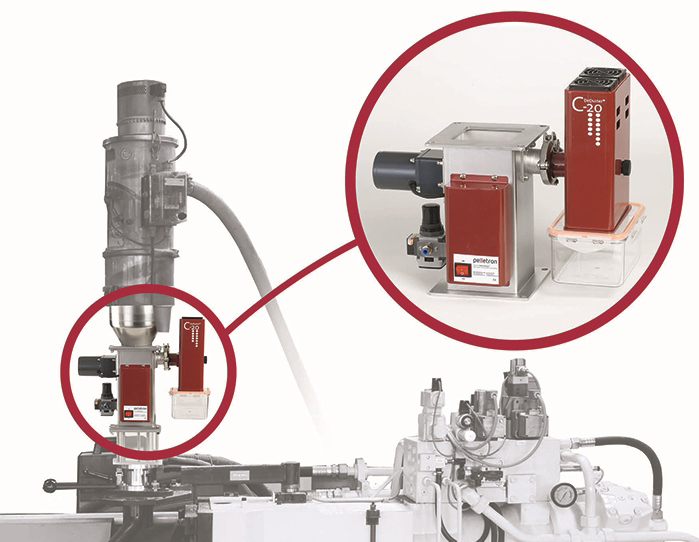
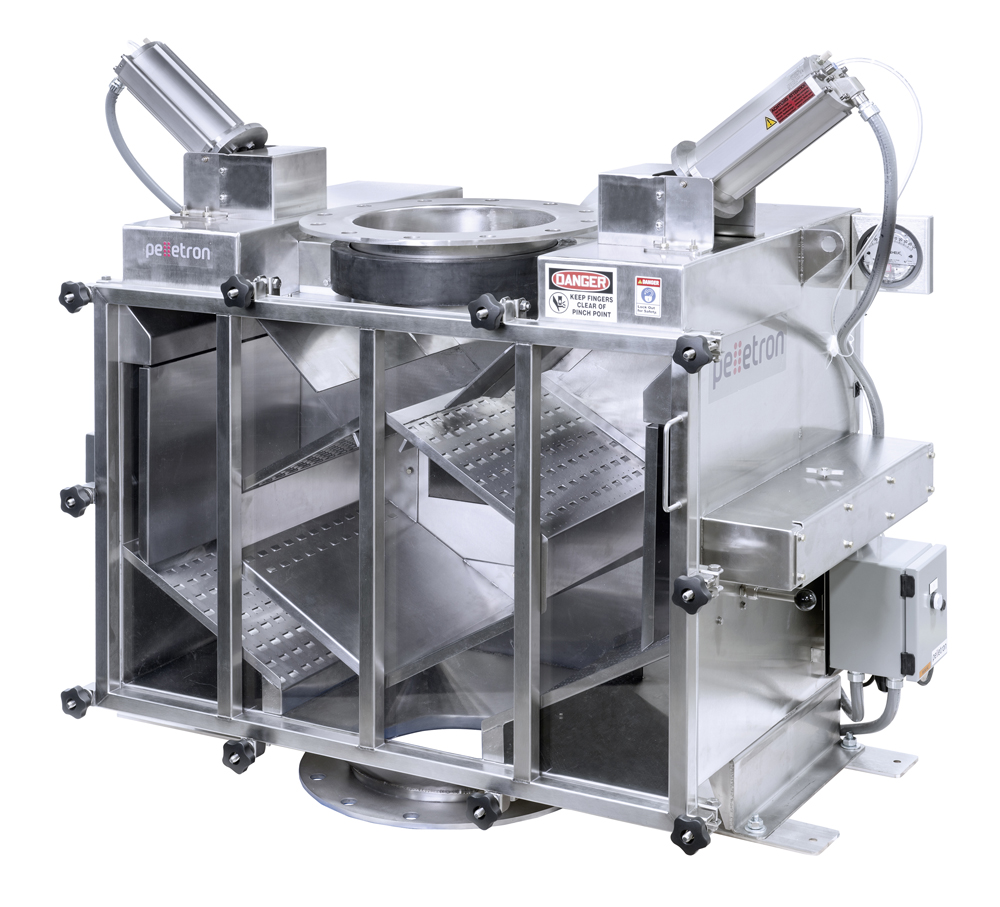
Booth W3383
Pelletron79 pelletron.htm is a leading provider of pneumatic conveying systems and components for the plastics industry. Pelletronsearch?q=pelletron introduces and displays new DeDusters and the pellcon3® conveying process at the NPE 2015 show in Orlando, Florida.
Pellcon3® – the new gentle conveying process
Visit our booth and see the new pelcon3® in operation. The pressure conveying process is designed for large conveying capacities, specifically for Compounders and Plastics Manufacturers, consisting of the three components STRANDPHASE®, Pellbow® and DeDuster®. Gentle conveying, low attrition and clean material are the main features besides the economical investment costs.
Pellcon3® sketch
The pellcon3 process consists of three major conveying components, STRANDPHASE® conveying, the special pipe bend Pellbow® and the DeDuster®. The system is in operation at the show.
STRANDPHASE® conveying
Working principle of the new, patented RC-series DeDuster®
Pellbow® working principle
This new process was developed for the plastics manufacturing and compounding industry. Selecting a pneumatic conveying system is important for economic and reliable operation of any plastics manufacturer or compounder. Poorly designed systems lead to plant-wide inefficiencies and high maintenance costs. When designing pneumatic conveying systems, many design parameters must be considered. The length of the system, numbers of elbows and varying material properties all have a significant influence on the determination and sizing of a pneumatic conveying system.
Cost savings with pellcon3®
Existing dense phase and dilute phase systems may be upgraded to incorporate pellcon3® technology. Upgrading an existing system to pellcon3® provides a quick return of investment. Besides the savings of 20% to 30% compared to dense phase conveying at new plant installations, pellcon3® provides lower operation costs and better product quality, which results in higher resin market prices.
Developed for injection molders – the new lightweight DeDuster®
Pelletronsearch?q=Pelletron+site:bulk online.com&hl=de&newwindow=1&safe=active&client=safari&rls=en&prmd=ivns&source=lnms&tbm=isch introduces the C-20, a completely new DeDuster® (patent pending), developed specifically for injection molding processes.
• Excellent cleaning/dedusting results
• Low construction height – 9.5in (240mm)
• Lightweight design – 20lbs (9kg)
• Economical investment costs
Removing dust and streamers prevents the creation of black or weak spots in finished products and results in reduced scrap rates, higher quality parts and improved profit.
C-20 DeDuster® installed on Injection Molding Machine
The design:
The C-20 DeDuster® weighs 20lbs (9kg) and requires only 9.5in (240mm) for installation between the hopper loader and inlet hopper of an injection molding machine. It features stainless steel construction, 110 or 220V operation and only consumes 2-3CFM (3.4-5m3/h) compressed air at 20-30psi (1.5-2bar) pressure. The C-20 DeDuster® is designed for a nominal product flow rate of 50lbs/h (~20kg/h) at 30lbs/ft3 (560kg/m) bulk density. Flow rates up to 70lbs/h (30kg/h) are possible for products with higher bulk densities.
How it works:
The design of the C-20 builds upon the features of the proven mini-DeDuster® Series. The product inlet has an integrated agitator to reduce “bridging” and the Venturi design maximizes dust removal performance and minimizes carryover of good product into the dust collector. It operates with compressed air supplied directly from the plant air supply instead of from a separate fan.
Inside the unit, the compressed air is split into two air streams for optimal removal of dust and streamers, and an ionizer is used to release the electrostatic bond between the pellets and the dust. The cleaning air blows the removed fines and streamers into two mini-cyclones, which separate them from the air. The separated contaminants are collected in a clear dust collection box and the cleaned air is filtered and released to the atmosphere. For creation of a negative pressure in the entire device, outside air is pulled in through a filter-protected opening.
New DeDuster design for high capacity loading of up to 150t/h
XP-series DeDuster® with automated inlet device
Visit our booth and see the XP-360 DeDuster® with the new automated inlet device in operation.
Pelletron DeDuster XP360
Saving costs and simplifying the operation was the inspiration for this new development (patent pending). This DeDuster® feature was designed for cleaning large capacities of plastics pellets in Plastics Producer plants from 40,000 lbs/h (18 t/h) to 330,000 lbs/h (150 t/h) at bagging, truck and railcar loading. The new device eliminates the use of expensive and heavy rotary valves that are normally used for feeding product into the DeDuster®. The automated inlet deflectors move to adjust the product flow to the desired flow rate, evenly distribute product over the wash decks of the DeDuster® and can shut down the product flow completely. Rugged pneumatic actuators with integrated positioners move the inlet deflectors to any position based on a control signal from the plant DCS.
Tel.: +1.717.293.4008
e-mail : www.pelletroncorp.comwww.pelletroncorp.com
More information on Pelletron79 pelletron.htm
Google Search - Websearch?client=safari&rls=de de&q=Pelletron+site:bulk online.com
Google Search - Imagessearch?q=Pelletron+site:bulk online.com&hl=de&newwindow=1&safe=active&client=safari&rls=en&prmd=ivns&source=lnms&tbm=isch
Pelletron on the Portalsearch?q=pelletron
Please watch this videopelletron xp series deduster with automated inlet device.html
Pelletron is a "bulk-online Leader"bulk online leaders and a "bulk-online Sponsor"sponsors ■